Are you still struggling to find the right packaging machine?
There are many kinds of automatic packaging machines including premade bag machines, pillow machines, Coffee Capsule Packaging Machine, Tea Bag Packaging machines, Vertical Form Fill Seal Packing Machines, and Carton Packing Machines. Tailoring to your specific needs, It has expanded to over a dozen series and nearly a hundred variants. Designed for versatility, machines adeptly handle granular solids, powders, liquids, and mixtures, suitable for small to large-scale packaging.
Serving diverse industries like food, chemical, pharmaceutical, and more, these machines streamline processes like weighing, counting, feeding, filling, and bag making. They not only enhance work efficiency but also significantly reduce costs, making them an ideal choice for businesses seeking to optimize their packaging operations.
Chapter 1 Packaging Bag Material Compatibility
Does the machine support the use of the packaging materials I plan to use?
When considering packaging machines, it’s crucial to ensure they are compatible with the packaging materials you intend to use. Modern packaging options are diverse, and tailored to the unique preservation needs of different products.
For instance, confectionery and cookies often use BOPP/CPP materials, known for their transparency and moisture resistance.
Instant noodles and snacks typically utilize BOPP/PE structures, providing excellent heat sealing and protection against moisture and oxidation.
Foods like puffed snacks or oily items are often packaged in PET/AL/PE, offering superb barrier properties against air, moisture, and grease, preserving freshness and taste. High oxygen barrier requirements, such as for meats or cold fruits, are met with PET/VMCPP materials, ensuring light blocking and airtight packaging.
For frozen or vacuum-packed foods, NY/PE materials are preferred for their durability in low temperatures.
Additionally, KOP/CPP materials are ideal for foods like mooncakes or fried snacks that require aroma preservation. Conventional packaging often involves LDPE or HDPE materials, chosen based on pressure requirements and known for their practicality and flexibility in various commodity packaging. Each material choice plays a vital role in maintaining the quality and appeal of the packaged product.
Please distinguish what type of product bag you need to package.
Chapter 2 How to Distinguish between Categories of Packaged Products?
Before purchasing a packaging machine, understanding the proper categorization of packaged products and efficient packaging methods is critical. Here are some step-by-step guidelines:
Distinguish between packaging product categories:
By function: firstly, according to the purpose of product packaging, such as transportation packaging (focusing on protection, shock, and pressure resistance) and sales packaging (focusing on appearance appeal, brand display).
Material includes cartons, plastic bags, metal cans, glass bottles, and composite material packaging.
By form: solid, liquid, powder, or granular products in different forms require different filling methods and sealing technology.
By industry: food, drugs, cosmetics, electronic equipment, and other industries have different packaging standards and requirements.
Quickly identify packaging needs:
Product Characteristics: Consider product size, weight, shape, and special storage requirements (e.g., moisture-proof, light-proof, refrigerated).
Productivity: Calculate the number of packages per day or hour and select a packaging machine with the appropriate capacity.
Cost control: Consider the cost of packaging materials, equipment investment, and operating costs to optimize the overall economic efficiency.
Environmental requirements: Follow national and regional regulations on green packaging, select biodegradable materials and energy-efficient packaging machinery.
Formulate the inquiry content:
Clearly describe the product information: including product type, size, weight, and expected packaging style.
A description of packaging requirements: packaging speed, degree of automation, additional functions required (labeling, heat shrinkage, etc.).
Propose quality and certification requirements: e.g. ISO certification, CE certification, etc. to meet the standards of the target market.
Consult after-sales service: to understand the warranty period, spare parts supply, installation and commissioning, operation training, and so on.
Request sample packaging service or reference cases, and ask for quotation and delivery time.
Send inquiry to the manufacturer:
After collecting and organizing the above information, you can send the specific requirements to potential suppliers of packaging machinery and equipment by email, online inquiry form, etc., and request them to provide corresponding solutions and quotations. At the same time, you should also pay attention to the other party’s market reputation, customer evaluation, and successful cases to ensure the reliability of cooperation.
Please distinguish what type of product you need to package.
Chapter 3 The Components of a Packaging Machine
The components of a packaging machine usually include several key parts, and the specific structure and function can vary depending on the different packaging needs and levels of automation. The following is an overview of packaging machine components and their functions in a general sense.
Feeding system:
– Storage hopper: used to store raw materials to be packaged, such as granules, powders, or liquids. – Actuating force-feeding equipment (e.g. vibratory pan, belt feeder): responsible for supplying the material in the hopper evenly and continuously to the next step in the process.
Weighing section:
– Weighing hopper: connected to a weight sensor, it realizes quantitative packaging by accurately measuring the weight of the material loaded into the hopper. – Weight sensor: detects and transmits the weight of the material in the hopper to the control system in real-time.
Pouring/filling device:
– Discharge gate/valve: controlled by a pneumatic cylinder or another driving mechanism to ensure accurate discharging into the packaging container according to the weighed weight.
Bag-making system (for automatic packaging machines):
– Packaging material unwinding and molding parts: Packaging materials such as laminated film, non-woven fabric, paper-plastic film, etc. are heated and melted into bags here.
Sealing system:
– Cutting and heat sealing components: the cutting, top sealing, bottom sealing, or side sealing of the bags are completed.
Control system:
– Electronic control device: including PLC, touch screen, and other components, responsible for the whole machine’s operating instructions, data processing, and the coordination of the components.
Auxiliary components:
– Clip the bag, and push the bag device: to help fix the bag in order to facilitate the lower material and sealing operation.
– Vibrating platform: helps to distribute the material flatly after filling and reduces the volume error.
Conveyor System: – Finished products after packaging can be collected and organized by conveyor belt.
Chapter 4 Commonly Used Optional Equipment
Packaging machine options are a series of additional or supporting equipment designed according to different packaging needs and production environments, their main role is to optimize the packaging process, improve production efficiency, ensure a stable supply of materials, and achieve automation.
Platform
As a basic support structure, the packaging machine platform is used to install the main machine and other ancillary equipment, ensuring that the entire production line is well laid out and stable.
It may also provide space for workers’ operation and maintenance.
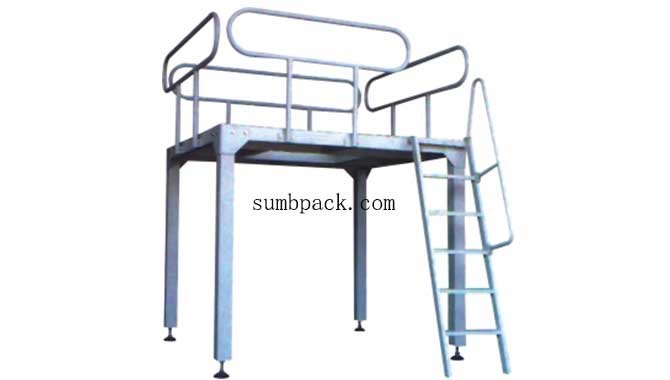
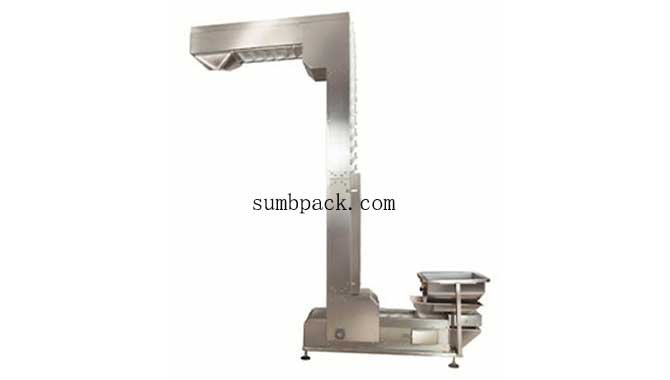
Z Type Conveyor
It is a kind of equipment that can realize the change of conveying materials in vertical direction or multiple plane angles, especially suitable for the occasions when space is limited but the materials need to be lifted from low to high and then into the packaging machine.
It is characterized by horizontal-vertical-horizontal multi-stage combination conveying, adapting to a variety of materials, including powders, granules, etc., and can adjust the feeding volume by controlling the speed of the rotary hopper.
Powder Screw Feeder
It is commonly used to continuously and uniformly convey powder, granule or other loose materials from the storage container to the inlet of the packing machine. It has the advantage that the conveying process is well sealed to avoid dust contamination, and the conveying speed and material flow rate can be controlled by adjusting the rotational speed of the screw body.
Conveyor belt or conveyor system to convey the finished products: after the packaging is completed, these devices are responsible for conveying the packed finished products from the output end of the packaging machine to the palletizing area, packing area or the next step of processing smoothly and quickly, which helps to reduce the cost of manual handling, improve the production beat, and ensure the continuity and stability of the production line.
In summary, the selection of these devices can greatly enhance the overall performance of the packaging line, reduce labor intensity, ensure product quality, and achieve a higher degree of automated production and logistics management.

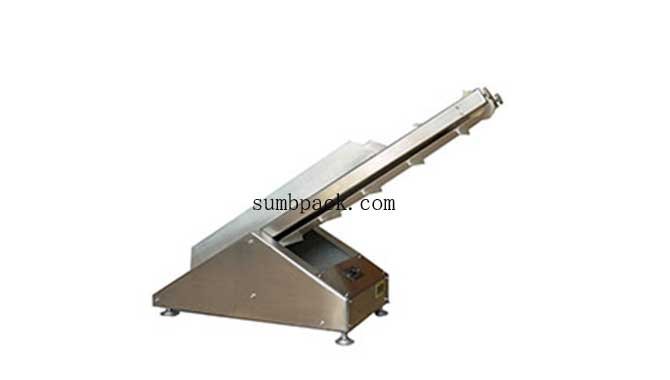
Small Output Conveyor
It is a kind of equipment that can realize the change of conveying materials in vertical direction or multiple plane angles, especially suitable for the occasions when space is limited but the materials need to be lifted from low to high and then into the packaging machine.
It is characterized by horizontal-vertical-horizontal multi-stage combination conveying, adapting to a variety of materials, including powders, granules, etc., and can adjust the feeding volume by controlling the speed of the rotary hopper.
Air Compressor
An air compressor is a device that converts electrical or mechanical energy into gas pressure energy.
It works mainly by compressing air to increase its pressure and storing it in a storage tank, and then supplying it to a variety of equipment or systems that need to use compressed air.
Compressed air is widely used in a variety of fields such as tool drives (e.g. pneumatic wrenches, paint spray guns, etc.), instrumentation control, pneumatic valves, blowing and cleaning, and so on.
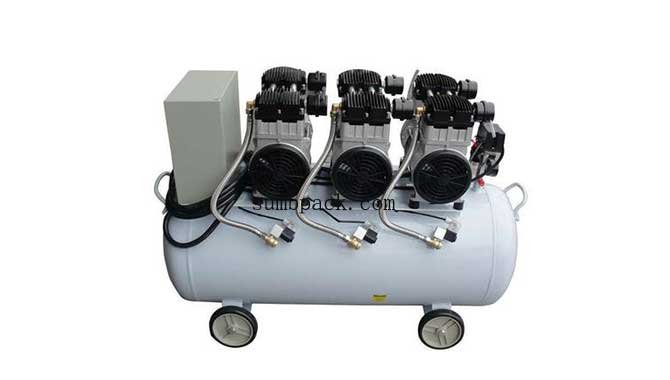
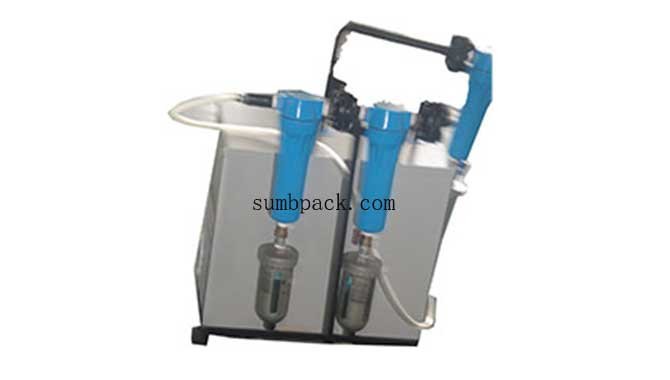
Nitrogen Gas Generator Drier
A nitrogen generator is a device used to produce nitrogen on site. Typically, a nitrogen generator will first utilize an air compressor to provide compressed air at a certain pressure, and then efficiently separate high-purity nitrogen from the air through pressure-variable adsorption (PSA) technology or membrane separation technology. As an inert gas, nitrogen has important uses in food preservation, chemical synthesis, electronics industry, oil and gas extraction, and metal heat treatment.
To summarize, an air compressor is used to generate and store compressed air, a vacuum pump is used to extract gas to create a vacuum environment, and a nitrogen generator is a device designed to produce high-purity nitrogen.
Volumetric Cup Filler
They can only weigh granular items smaller than a peanut, such as rice, sugar, salt, but some customers choose to use them for powders that do not raise much dust, such as laundry detergent and coffee powder. Turntables are the most affordable of the three types of granular weighing devices, but they are also the least accurate because they utilize volume for weighing.
Remark: If the weighing range is too large, another measuring cup is required. For example, if a customer needs to weigh 50-60g and 200-300g of granular product, then two sets of measuring cups are required.
Packing small granules need to add valves to prevent the material from leaking out.
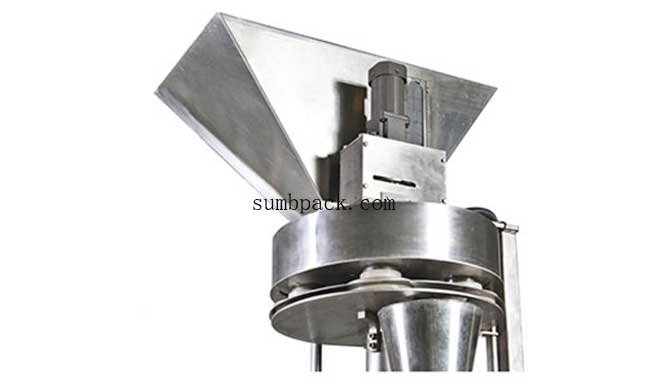
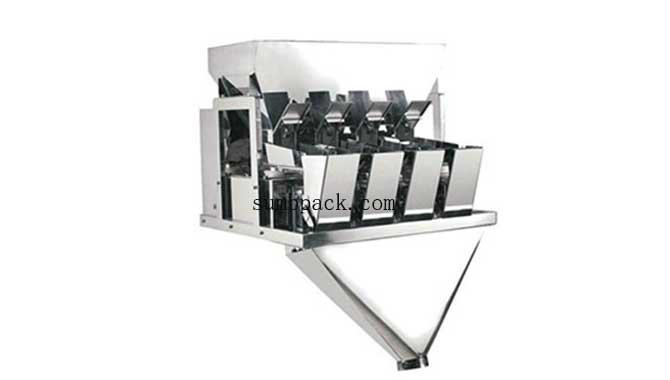
Linear Balance Weigher
Like the Volumetric Cup Filler, Linear Balance Weigher can only weigh granular items smaller than peanuts, such as rice, sugar, salt, but also some customers choose to use it to pack powder with little dust, similar to laundry detergent, coffee powder.
Linear Balance Weigher are more accurate and expensive than turntables, and are available in 2-head and 4-head versions.
Multihead Combination Weigher
Granules, potato chips, pickles, etc., with the highest accuracy, Multihead Combination Weigher: Multihead Combination Weigher can weigh a wider range of products than carousel and linear weigher, suitable for weighing all kinds of large and small particles, such as puffed food, hardware, flakes, long regular or irregular materials, dumplings, fruits and vegetables can be weighed with Multihead Combination Weigher. Accuracy and price are higher than turntable and linear weighing. Generally the multi-head combination weigher needs to be supported by a platform.
Commonly, there are 10-head weigher, 14-head weigher, 16-head weigher, 20-head weigher, etc. 10-head weigher and 14-head weigher are also divided into 1.6L hopper, 2.5L hopper and 5L hopper, which can be selected according to the size of materials and the capacity of each package.
Multi-head combination weigher: If you need to weigh sticky, watery materials, such as QQ candy, salad, etc., the surface of the weigher should be added with patterned plate and sprayed with Teflon.
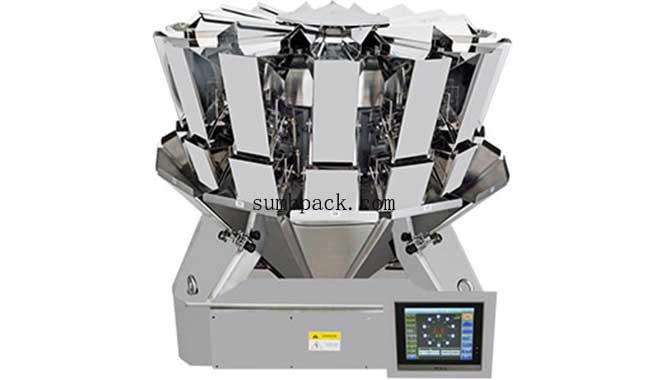
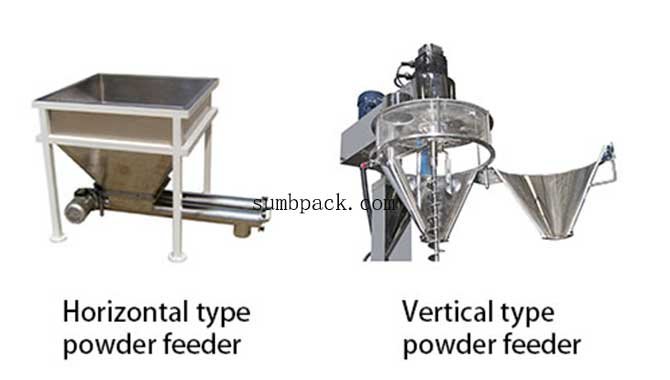
Powder Metering Auger Filler
Mainly divided into horizontal (left) and vertical (right), the generally small vertical machine with a horizontal powder feeder, is suitable for weighing rough powder.
A vertical powder feeder is larger than a horizontal one, and you can choose a vertical powder head for larger grams per package.
Screw packing usually has a screw. If the weighing range is large, in order to weigh accurately, another screw is needed. For example, 10g 16g with a screw, 200g 380g 400g with a screw.
Liquid Piston Pump
Weighing sauces and liquids, liquid pumps: mainly divided into self-priming pump (left) and sauce pump (right), self-priming pumps are suitable for weighing liquids with good fluidity, such as water, milk, juice, etc.
Sauce pumps are suitable for weighing viscous liquids with general fluidity, such as ketchup, jam, honey, peanut butter and so on.
If the liquid is too viscous, you need to add heating and stirring device.
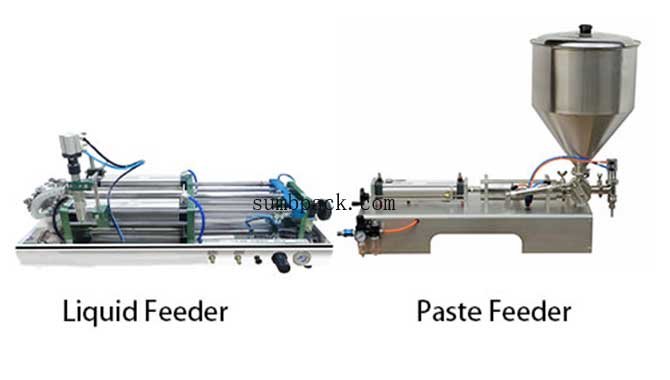
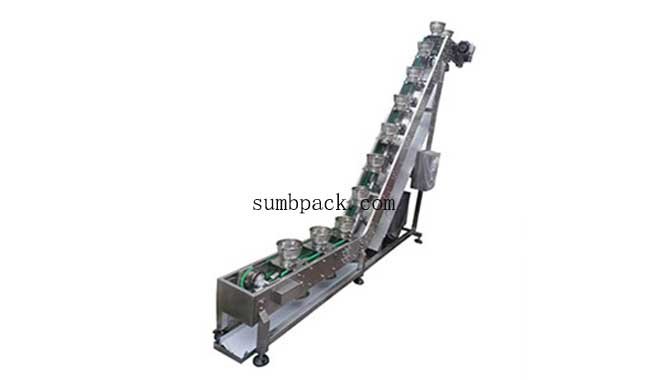
Hopper
Artificial chain hopper usually refers to the parts on the chain hopper conveyor, which is a kind of mechanical equipment used for conveying all kinds of loose materials. The role of chain hopper is to:
Carrying materials: Chain bucket is one of the key parts of the conveyor, which forms a continuous closed loop structure by connecting with the traction chain. During the conveying process, the chain hopper runs around the track, loads materials in the open part at the bottom, and lifts or pans the materials from the loading point to the unloading point smoothly with the movement of the chain.
Strong adaptability: Chain Bucket Conveyor is suitable for a wide range of material placement due to its unique design.
Particle Vibrating Disk
It is mainly used in automated packaging processes in industries such as pharmaceuticals, food, electronic components and small hardware accessories.
Accurate Counting: Through vibration, photoelectric sensing or mechanical sensing technologies, the counting tray can accurately count tablets, capsules, candies, chocolate beans, nuts, seeds or other small granular items to ensure that the number of granules in each bag or box of products meets the preset standards.
Orderly Arrangement and Filling: The counted particles are fed in a certain order and at a certain speed into the subsequent packaging stages, such as filling tubes, packaging films or bags, to realize a quantitative and orderly filling process.
Improve production efficiency and quality: the use of counting trays packaging machine significantly improves the degree of production automation, reducing manual errors, enhance production efficiency, and improve the consistency and accuracy of the product packaging, in order to meet industry regulations and consumer demand for product quality.
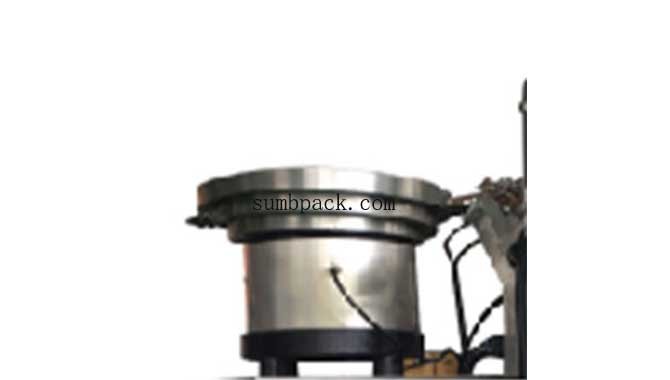
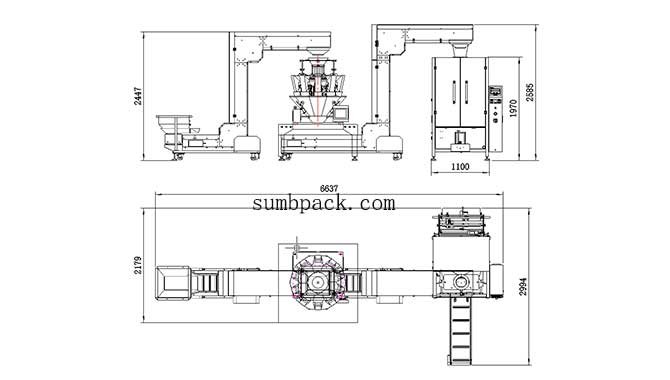
VFFS (Vertical Form Fill Seal) Packaging Machine
Versatility: Can handle multiple types of packaging materials.
Efficiency: High-speed operation with less manual intervention.
Sealing Quality: Provides strong and consistent seals.
Automatic packaging machine with bag-making function, mainly divided into two categories: big vertical machine and small vertical machine, according to the different packaging materials, it can be matched with different weighing devices: respectively, turntable, linear weighing, multi-head weighing, powder head, liquid pump, chain hopper, counting disk.
1. ONE machine can only do a kind of bag type (back seal, three-side seal, four-side seal, triangular bag), for example, a customer wants to pack ketchup, both three-side seal bag type, but also to do the bag type of back seal bag, then he can only buy two machines, one bag type is the three-side seal, one bag type is the four-side seal
2. Formers: a vertical machine is generally standard with a set of formers, the width of the bag can not be changed, but the length of the bag can be adjusted. If the width of the bag changes, then you need to set up a separate formers. For example, a customer’s bag size is 50mm * 70mm, 120mm * 150mm, two bag sizes, bag width is not the same, then you need another set of molding machine.
3. Vacuum device: small vertical machine can not be added vacuum device, large vertical machine can be added.
Large vertical machine: according to the different packaging materials, can be matched with different weighing devices: respectively, turntable, linear weighing, multi-head weighing, powder head, liquid pump, chain bucket, counting disk.
Large vertical machine all-in-one: common D-320D and D-420D, suitable for low plants, the host and ten-head weigher are directly connected together, no platform to stand on, then the customer does not need to buy a platform, but because there is no platform to stand up the ten-head weigher, the ten-head weigher vibration occurs during operation, which will have an impact on the accuracy of each package.
Horizontal Premade Pouch Packing Machine
Precision: Offers higher accuracy in filling and sealing.
Simplicity: Easier to operate and maintain.
Footprint: More compact, ideal for limited space.
Fully automatic bagging machine, applicable to the packaging of pre-made bags without bag making function, is mainly divided into three kinds of single-station bagging machine, multi-station bagging machine and rotary bagging machine, according to the different packaging materials, it can match different weighing devices: respectively, turntable, linear weighing, multi-head weighing, powder head, liquid pump, chain hopper, and granule counting disk.
One bag feeder can match many kinds of weighing devices, for example, if a customer needs to pack both granules and powder, then it can match both granule weighing device (turntable/linear weigher/multihead weigher) and powder head.
You can choose to mix two kinds of materials to be discharged, or you can choose to discharged separately.
About coding: you can choose to use a ribbon coder, or play the steel stamps or inkjet printer (can not be used TTO: thermal transfer coder); bag length less than 150mm can not be added to the coding machine!
Generally choose to use the standard ribbon coding machine, inkjet printer price is high, but the best results!
Ribbon coding machine coding position: the general production date hit in the lower left corner of the bag position
Steel mark coding position: playing in the closure
About zipper height: the distance from the zipper to the top should be between 23mm-35mm.
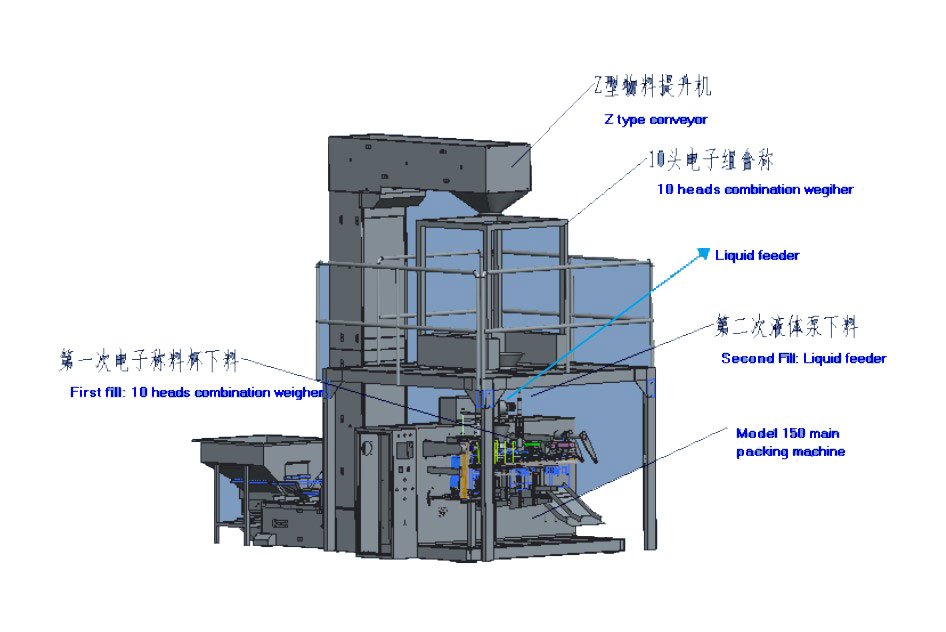
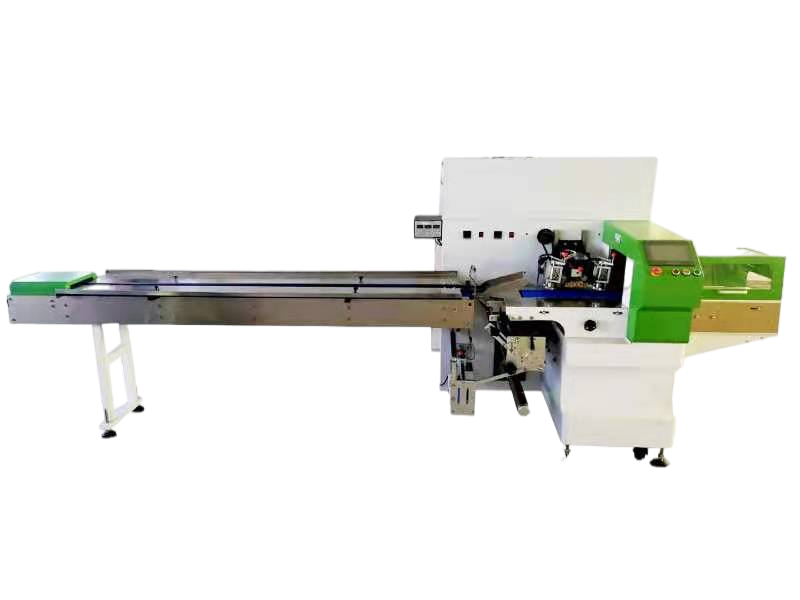
Flow Packaging Machine
Product Handling: Ideal for products that are fragile or require horizontal positioning.
Speed: Generally slower than VFFS but offers higher precision.
Material Usage: More efficient in material usage, reducing waste.
Suitable for packaging candy, cookies, bread, soap, masks, daily necessities or trays and other types of regular objects packaging, mainly divided into two categories of paper on the go and paper under the go.
Upper walking paper (roll film installed on the top): sealing at the bottom, suitable for packaging individual items, with trays, need to distinguish between positive and negative items, similar to the moon cake.
Pillow machine can be further divided into:
1. Ordinary machine (with frequency converter)
2. Plus three servo motors (cut bags more accurately)
3. Reciprocating (for larger products)
4. Special machine (candy packaging machine)
5. Tissue wrapping machine series
Lower walking paper (roll film installed below): sealing on the top, suitable for bulk, multiple items of packaging
Tea Bag Packing Machine
According to the different bag types can be divided into two types: three side seal tea bag machine and triangle bag tea bag machine.
Tea bag packaging machine is a type of machinery and equipment specially designed to automate the production of tea sachets.
These machines usually have the following functions:
1. Automatic filling: able to accurately measure and fill a quantitative amount of tea into each small tea bag made of filter paper or non-woven fabric.
2. Bag forming: cutting, folding, and heat sealing rolls of packaging materials (e.g., filter paper) into standard tea bag shapes with hanging threads and labeling holes.
3. Attaching threads and labels: laminating cotton threads or nylon threads on the tea bags, and automatically placing labels to facilitate the extraction of tea bags by consumers when making tea. which makes it easy for consumers to extract the tea bags when making tea.
4. Outer bag heat sealing: After finishing the inner bag sealing, some models can also seal the outer bag, i.e., put the individual tea bags into larger packaging materials and seal them.
5. Automatic counting and packing: Count the packaged tea bags automatically according to the set quantity, and pack or box them according to the required quantity.
Through these automated processes, the tea bag packaging machine greatly improves the efficiency and hygiene standard of tea production and is an economical and practical equipment choice in the tea processing industry and food industry.
D-12A Tea bag machine: inner bag only, with the line, with the label, no outer bag
D-12B Tea bag machine: inner bag, with the line, with the label, with outer bag
D-12T Triangle bag tea bag machine: inner bag, with line, with labeling
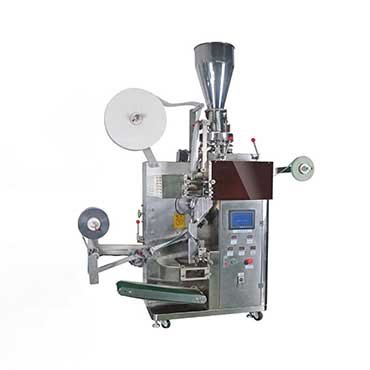
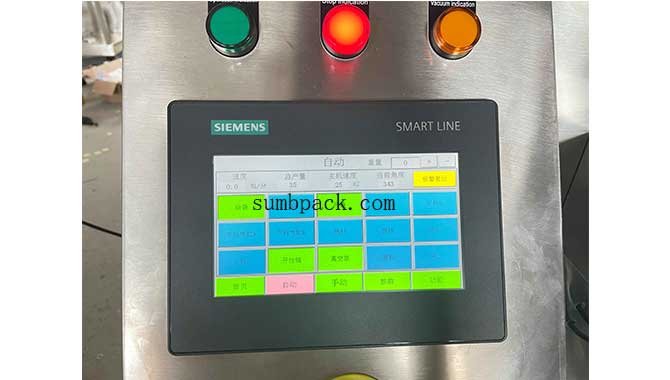
Control system
Operational stability: this refers to whether the equipment can maintain efficient, accurate and trouble-free when working continuously. Specifically include:
Technical parameters: to understand the maximum capacity of the equipment, operating speed and its performance throughout the work cycle of the performance is stable.
Control system: Whether advanced PLC or computerized control system can ensure accurate control of the equipment during a long period of operation and avoid downtime due to system errors.
Mechanical structure
Mechanical structure design: High-quality material selection, precise manufacturing process and reasonable mechanical design help to ensure the long-term stable operation of the machine in a high-intensity production environment.
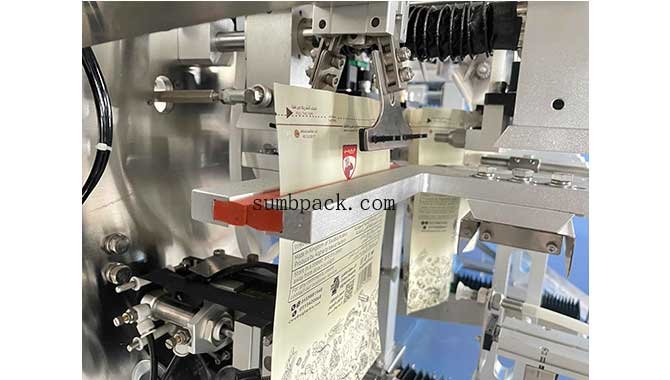
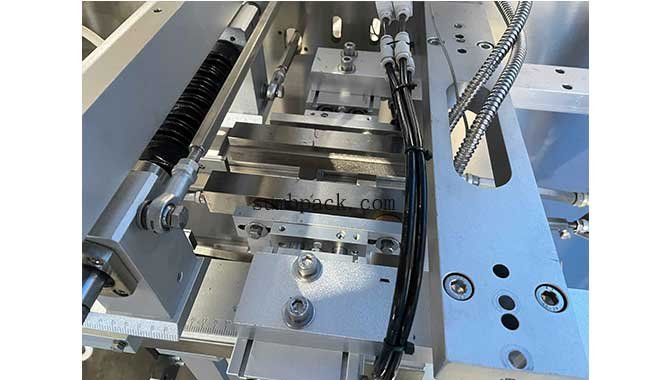
Components
Durability degree and failure rate:
Quality of components: The quality of key components such as motors, bearings, cylinders, heating elements, etc. directly affects the overall durability of the machine and the probability of failure.
Maintenance: Whether the machine has an easy-to-maintain design and the importance of regular maintenance to prolong the service life and reduce the failure rate.
Historical data and user evaluation: Checking the historical use records, customer feedback and industry reputation of the equipment can roughly assess its failure frequency in actual applications.
Working Schematic
Maintenance frequency and convenience:
Modular design: good packaging machines often adopt modular design, making the parts easy to disassemble, replace and repair.
After-sales service system: the after-sales support and technical services provided by the manufacturer, including quick response time, timeliness of spare parts supply and the provision of professional training and guidance, etc., will affect the efficiency of the repair of the equipment after a problem occurs.
Failure diagnosis function: modern packaging machines are often equipped with intelligent diagnostic systems, which can monitor and warn of potential failures in real time, reducing unplanned downtime and maintenance costs.
Combining the above factors, the buyer can examine the actual case of the equipment, ask the manufacturer to provide detailed performance test reports and fully understand the manufacturer’s after-sales service policy to fully assess the performance stability and durability of a packaging machine.
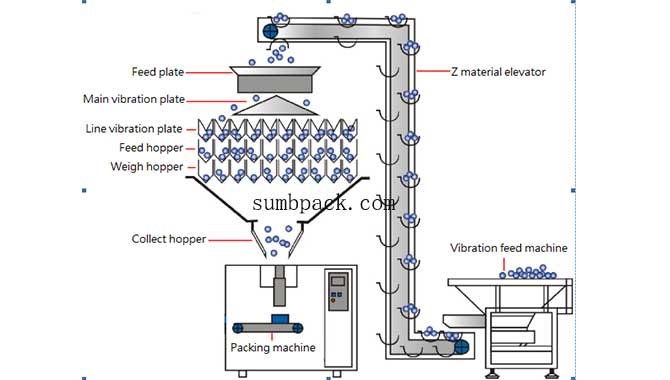
Price-performance Ratio
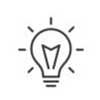
Compare different brands and models of packaging machines to choose the most cost-effective option within your budget.
Within a pre-determined budget, a value-for-money assessment involves in-depth research, comparison and analysis of different brands and models of packaging machines.
First of all, value for money does not only focus on the price of the product, but also examines a number of dimensions such as its performance, quality, durability, functional features, energy efficiency and after-sales service. For example, when comparing packaging machines, technical parameters such as packaging speed, accuracy, range of applicable packaging materials, ease of operation and expected service life need to be considered.
Secondly, the cost performance evaluation also needs to combine the above indicators with the selling price of the product. Even if a packaging machine is excellent in performance, but if its price is far beyond the budget and beyond the actual needs, then from the perspective of cost-effective, may not be the best choice. On the contrary, if a device although the price is relatively low, but its performance is stable, can meet the basic needs, and has a good reputation and perfect after-sales service, then the cost-effectiveness of this equipment may be higher.
In the end, by comprehensively weighing various factors, buyers are able to identify the most cost-effective packaging machine option within their budget, maximize the benefits of spending, and ensure that their investment will bring long-term, stable returns.
Evaluating the cost-effectiveness of a packaging machine from the perspective of after-sales service is an important part of determining its overall value. After-sales service includes but is not limited to the following aspects:
Maintenance services: examine whether the manufacturer provides timely and professional maintenance services, such as whether there is a specialized service team or designated maintenance outlets, how fast the response time, and the length of the warranty period. Good after-sales service can ensure that when the machine breaks down, it can be quickly resolved, thus reducing production losses due to equipment downtime.
Parts supply: to understand the manufacturer for the supply of parts, including the price of parts, accessibility and service life. In the long run, if the parts are reasonably priced and easy to replace, it will greatly reduce maintenance costs and improve the cost-effectiveness of the equipment.
Technical support and training: excellent after-sales will provide detailed operational training and continuous technical guidance, which is essential to ensure the efficient and stable operation of the packaging machine. Especially for the operation of complex or fast technology update equipment, good technical support can improve efficiency and avoid problems caused by improper operation.
Extended services: some manufacturers will also provide preventive maintenance, regular inspections, software upgrades and other value-added services, which can to a certain extent enhance the efficiency and service life of the packaging machine, thus affecting the cost-effectiveness of the equipment.
In summary, when evaluating the cost-effectiveness of packaging machines, quality after-sales service can not only reduce the subsequent use of the trouble and expense, but also effectively guarantee the full play of the performance of the equipment, so that the return on investment is maximized.
Summary
It’s not an easy thing to select the right packing machine, but with proper information, the process becomes more straightforward. Understanding the specific functions and requirements of your packing machine is key to narrowing down your choices. This article provides essential insights into what you need to know before purchasing a packing machine, ensuring that your decision is well-informed and tailored to your specific packaging needs.
To sum up, the weighing packaging machine, it’s core component is the weighing part, through the accurate weight sensing technology and self-unloading weighing hopper to realize the quantitative distribution of materials. The other parts work together to complete the whole packaging process. For vertical machines and bag feeders, different weighing devices can be matched according to different packaging materials: turntable, linear weigher, multi-head weigher, powder head, liquid pump, chain hopper, and counting disk.
Selecting the appropriate packaging machine is a critical decision for any manufacturing business. The choice can significantly impact operational efficiency, product quality, and overall profitability. This article aims to guide you through the key considerations when choosing a packaging machine, focusing on the differences between various types.
The main reason for the different types of packaging machines is to adapt to the various specific needs and processes of product packaging. Different packaging materials (e.g. solids, liquids, powders, granules, etc.), packaging containers (e.g. bottles, cans, bags, boxes, etc.), packaging requirements (e.g. sealing, protection, display, safety, hygiene standards, etc.) and production efficiency are the factors that determine the diversity and specialization of the design of packaging equipment.